Gears & Racks
Gear racks are used to change circular motion into straight-line motion. A gear rack consists of straight teeth carved into one side of a square or round rod, and it works together with a pinion. The pinion is a small cylindrical gear that meshes with the gear rack. In general, the combination of gear rack and pinion is referred to as “rack and pinion.” There are various applications for using gears.
We are confident in providing you with high-quality gear and racks. AGKNX distinguishes itself from other distributors by offering products at highly competitive prices and providing expert customer service with rapid response. For more information or to receive a product quote, please contact us, and we will be happy to assist you.
Types of Gears
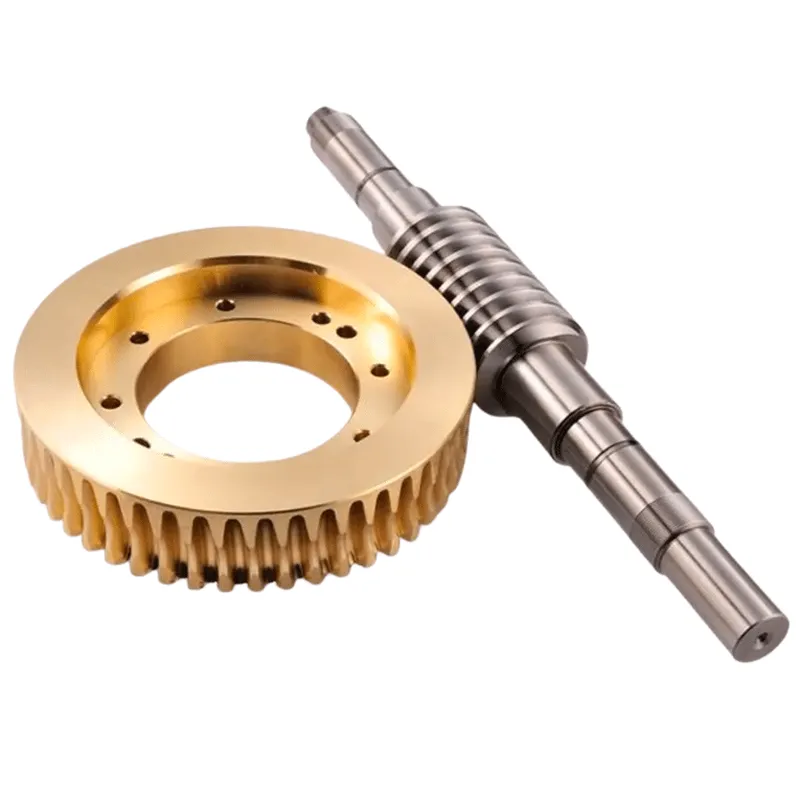
Worm Gears
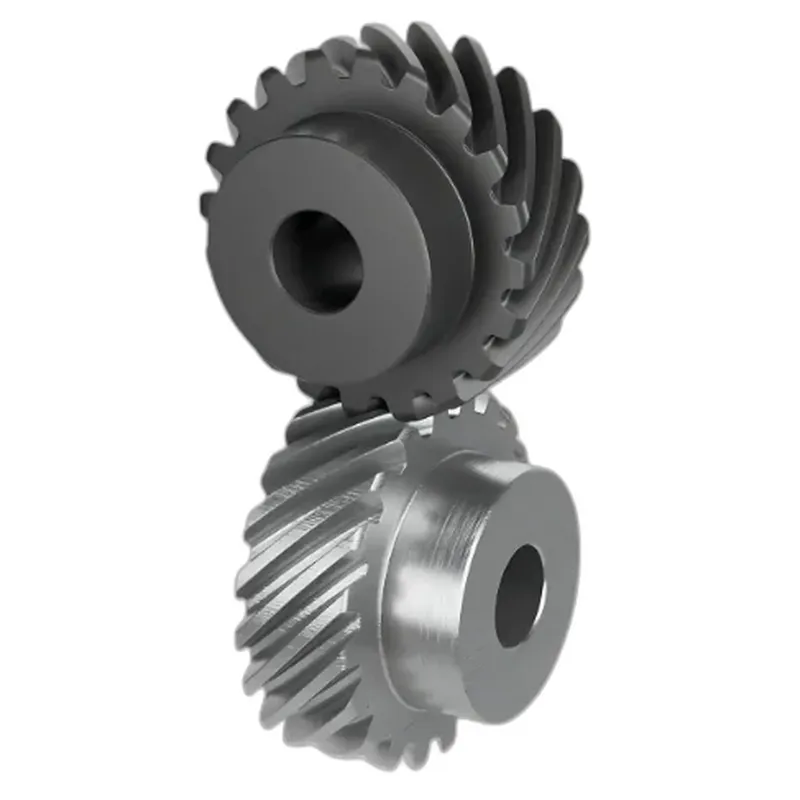
Screw Gears
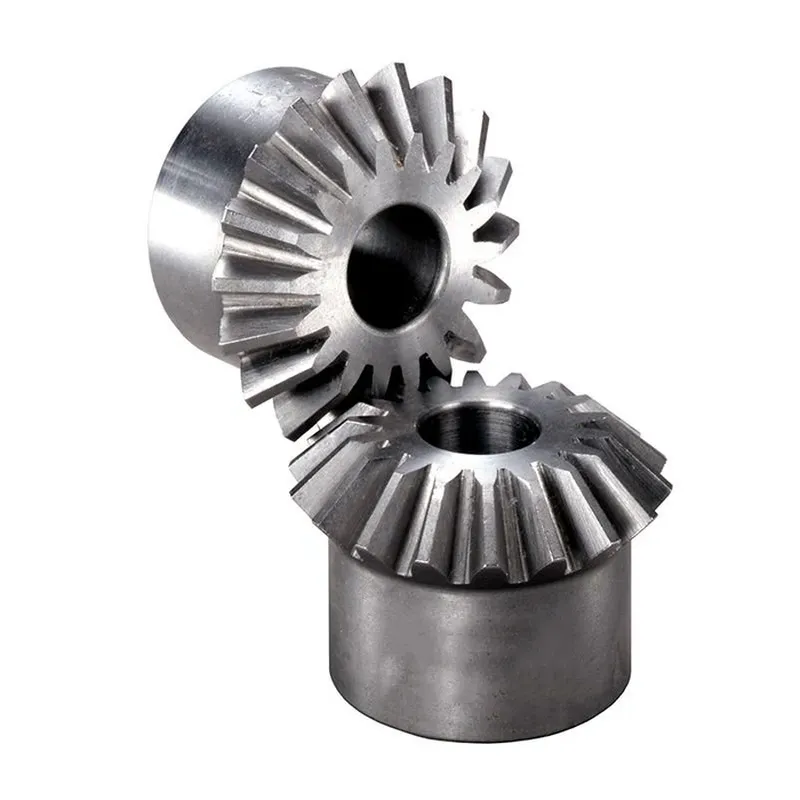
Miter Gears
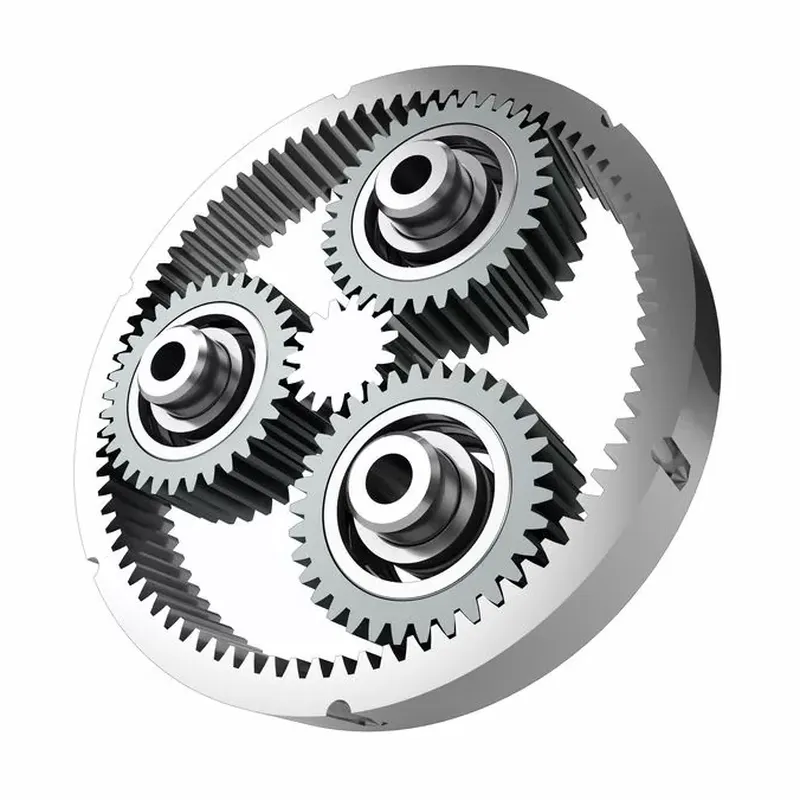
Planetary Gears
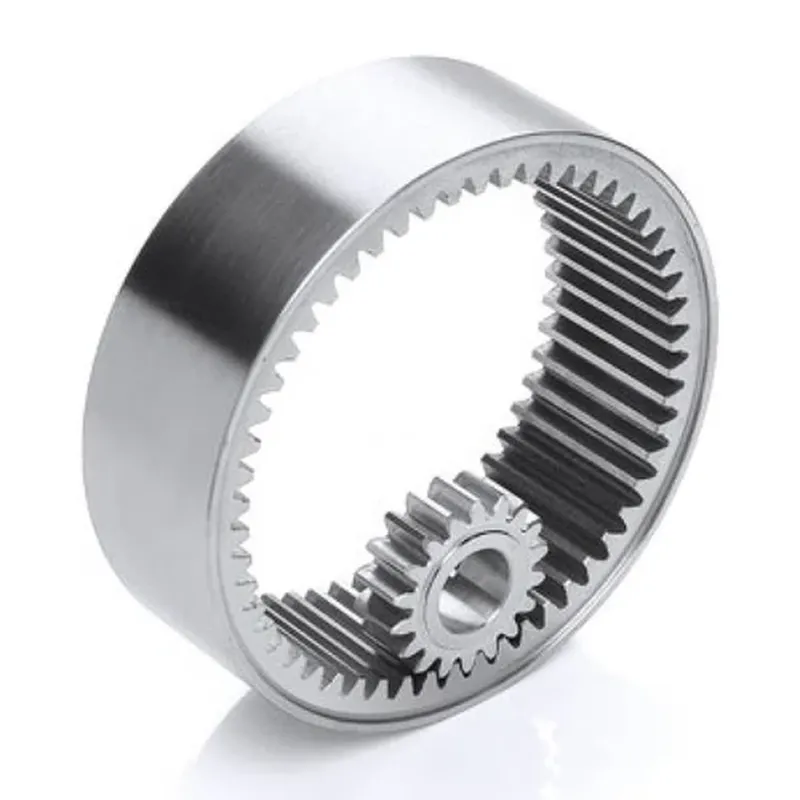
Internal Gears
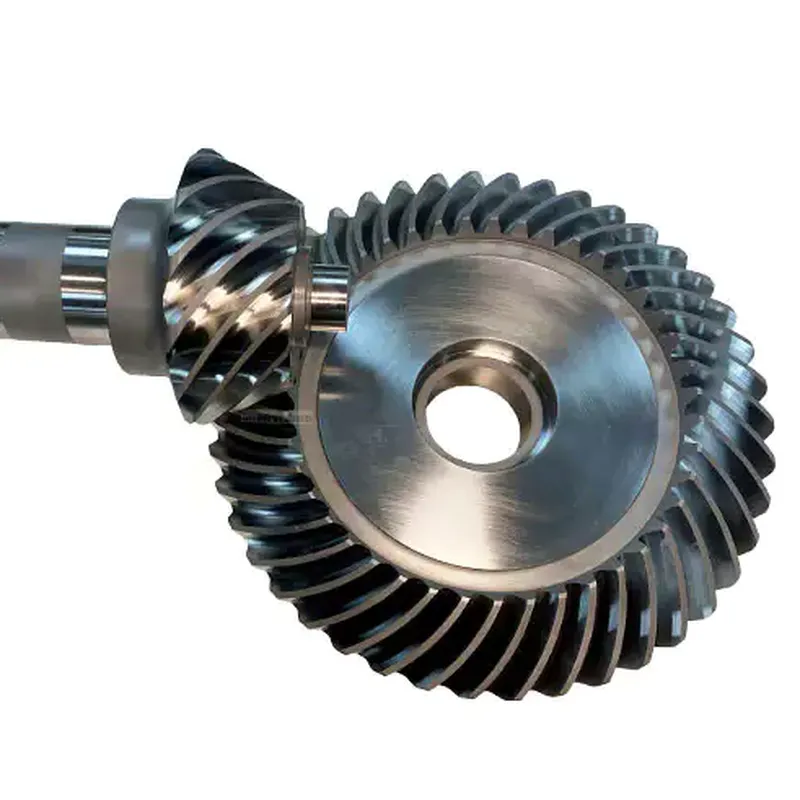
Hypoid Gears
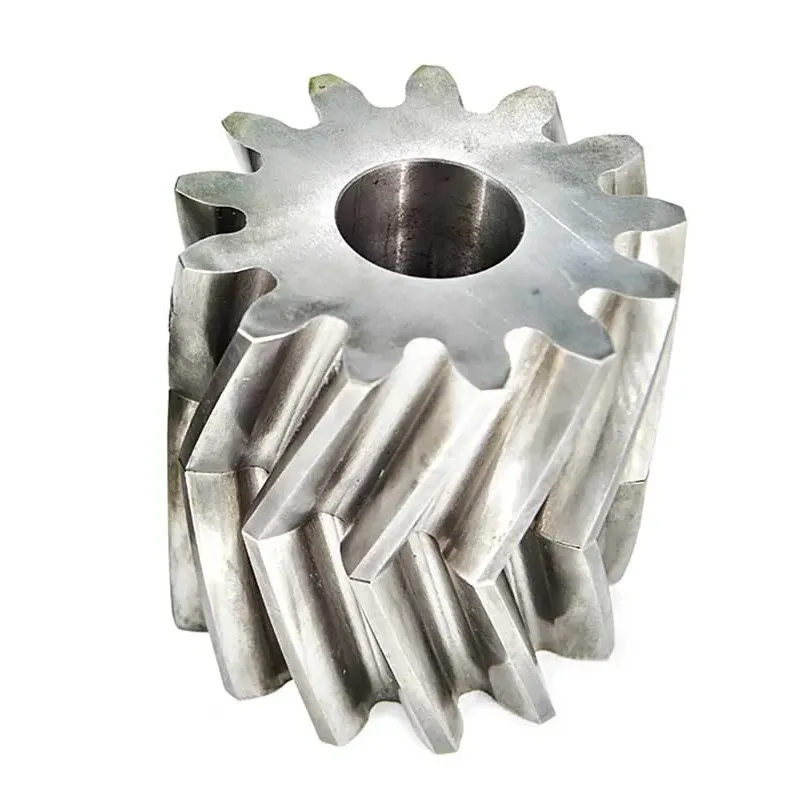
Herringbone Gears
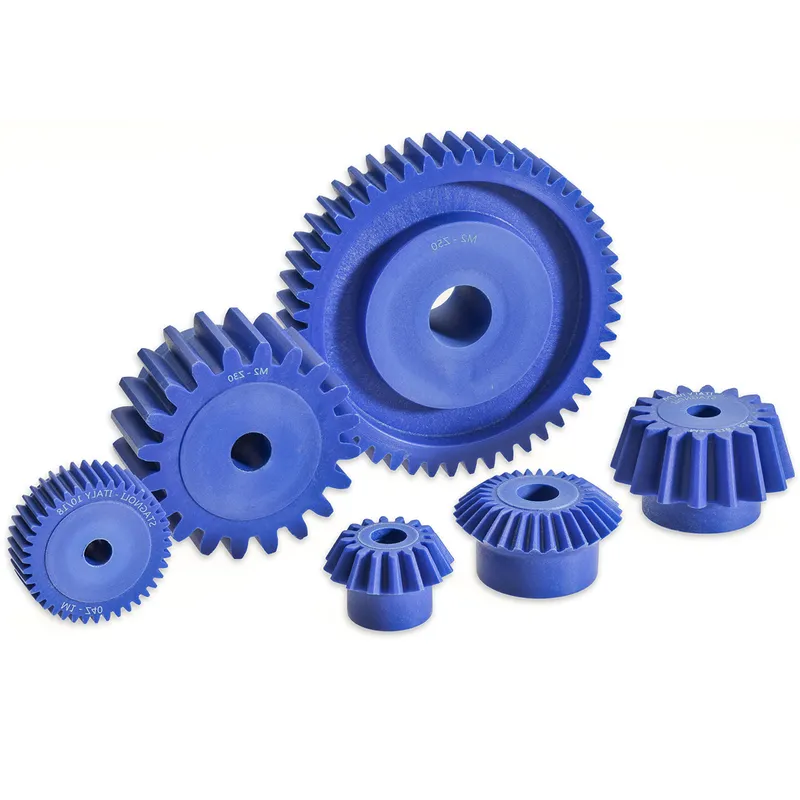
Plastic Gears
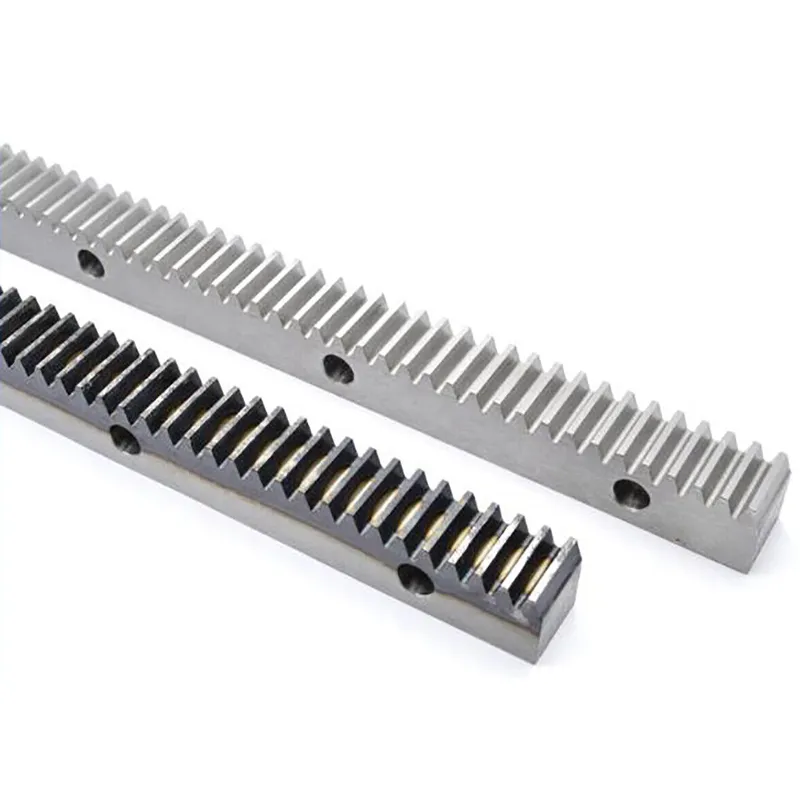
Gear Racks
Precision Gears and Racks for All Industries
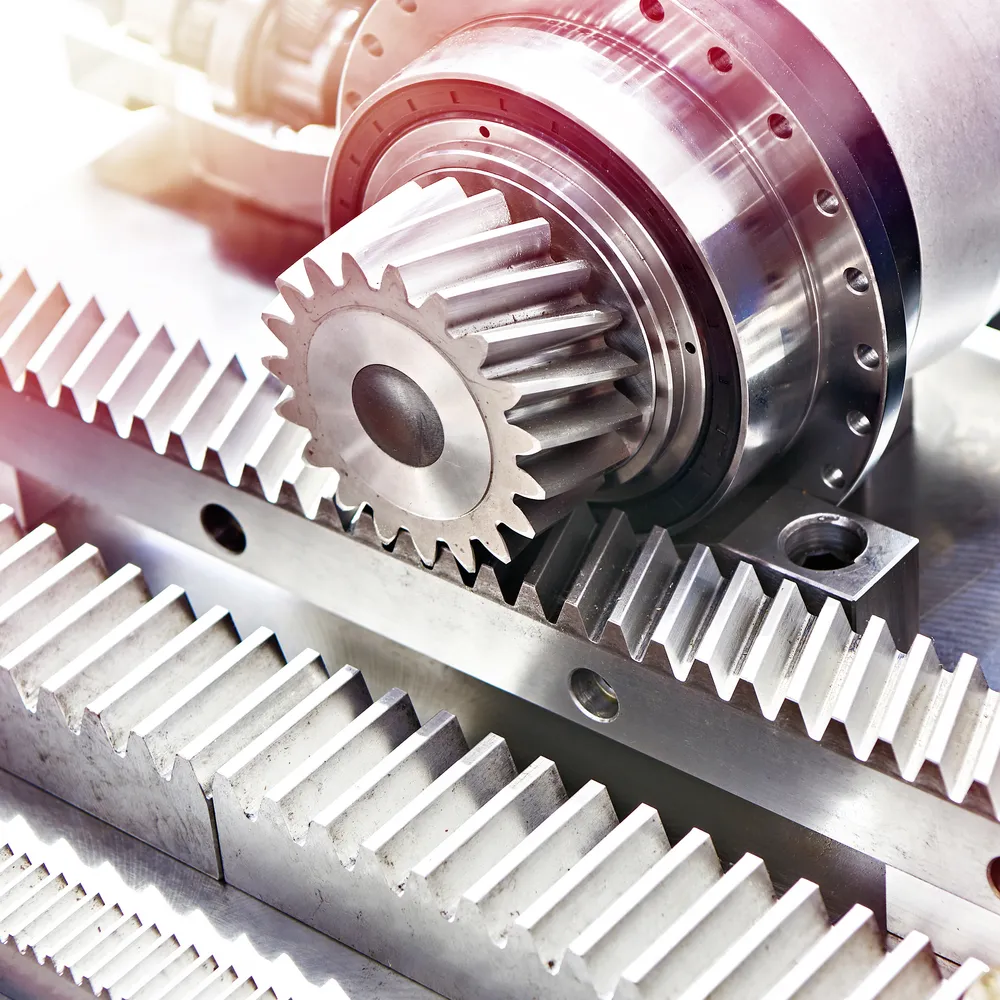
Gear Production Process
Blanking → forging → drilling → numerical control → Heat treatment → grinding machine → packaging
- Blanking: This initial step involves cutting raw material, typically steel or alloy, into circular blanks using shearing or sawing machines. The blanks are shaped to approximate the gear’s outer diameter, ensuring minimal material waste. Precision is critical to provide a suitable starting point for subsequent processes.
- Forging: The blank is heated and shaped under high pressure using forging presses or hammers to form a rough gear shape. This process enhances the material’s strength and grain structure, improving durability. Forging ensures the gear can withstand mechanical stresses during operation.
- Drilling: Holes are drilled into the forged gear blank to create bores or mounting points, using specialized drilling machines. Precision is vital to ensure alignment and fitment in assemblies. Coolants are often used to manage heat and extend tool life during this process.
- Numerical Control (CNC Machining): CNC machines precisely cut gear teeth and refine the gear’s shape using computer-controlled tools. This step ensures high accuracy in tooth profiles and surface finish, critical for smooth operation and efficient power transmission in mechanical systems.
- Heat Treatment: The gear undergoes heat treatment processes like quenching and tempering to enhance hardness and toughness. Controlled heating and cooling alter the material’s microstructure, improving wear resistance and strength to withstand high loads and prevent premature failure.
- Grinding Machine: Precision grinding refines the gear’s teeth and surfaces to achieve tight tolerances and a smooth finish. This step minimizes friction, noise, and wear during operation, ensuring optimal performance and longevity in demanding applications like automotive or industrial machinery.
- Packaging: Finished gears are cleaned, inspected, and coated with protective oil to prevent corrosion. They are then carefully packed in sturdy containers or crates to ensure safe transportation and storage, maintaining quality until they reach the end user or assembly line.
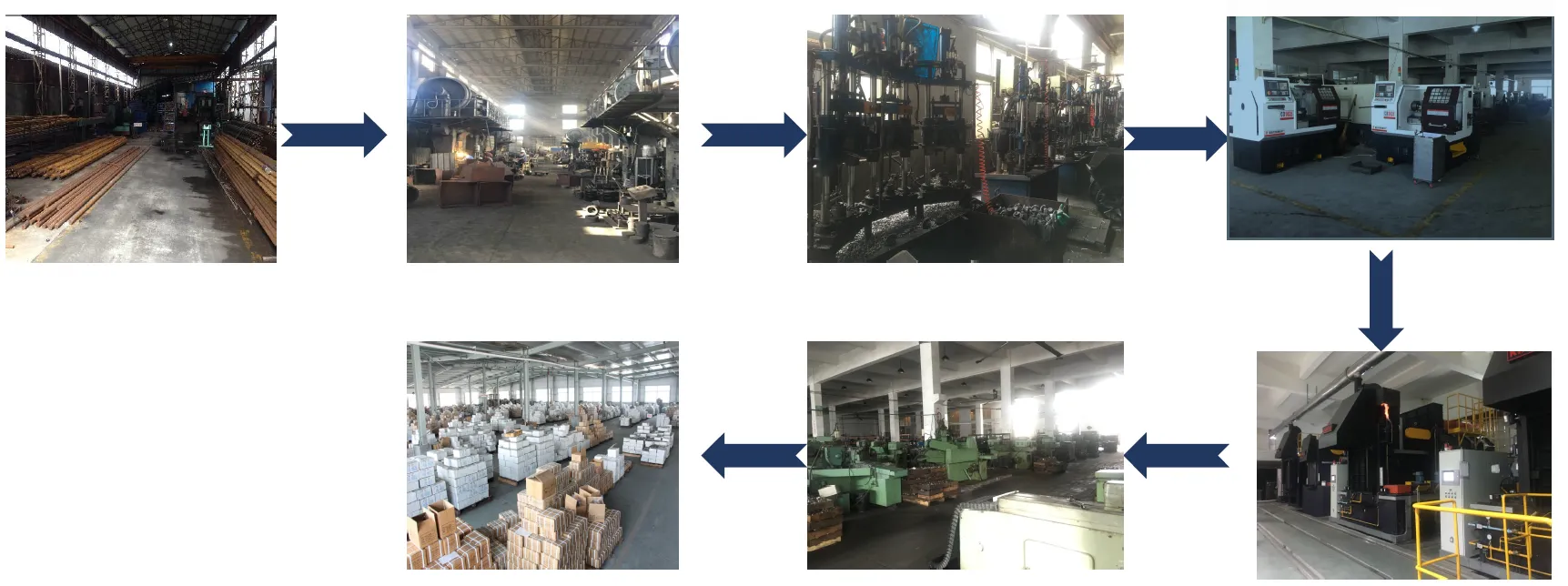
Common Materials of Gears
- Steel
- Carbon Steel: Widely used for its strength and affordability. Suitable for medium-duty applications (e.g., AISI 1045, 4140).
- Alloy Steel: Enhanced with elements like chromium, molybdenum, or nickel for higher strength, toughness, and wear resistance (e.g., 4340, 8620). Often used in heavy-duty or high-precision gears.
- Stainless Steel: Corrosion-resistant, ideal for harsh environments (e.g., food processing, marine applications). Common grades include 304 and 316.
- Heat-Treated Steel: Hardened or case-hardened (e.g., carburized or nitrided) to improve surface hardness and wear resistance while maintaining a tough core.
- Cast Iron
- Offers good wear resistance and damping properties, making it suitable for large, low-speed gears. Commonly used grades include gray cast iron and ductile iron.
- Cost-effective but brittle compared to steel
- Brass and Bronze
- Brass: Used in low-load, low-speed applications (e.g., clocks, small machinery). Corrosion-resistant and easy to machine.
- Bronze: Excellent for worm gears due to its low friction and wear resistance. Often paired with steel worms.
- Aluminum
- Lightweight and corrosion-resistant, used in applications where weight reduction is key (e.g., aerospace, robotics). Typically alloyed (e.g., 6061, 7075) for added strength.
- Plastics
- Nylon: Self-lubricating, quiet, and corrosion-resistant. Common in light-duty applications (e.g., printers, consumer goods).
- Acetal (Delrin): High strength and low friction, suitable for precision gears.
- Polycarbonate: Tough and impact-resistant, used in specific low-load scenarios.
- Plastics are often reinforced with glass or carbon fibers for added strength.
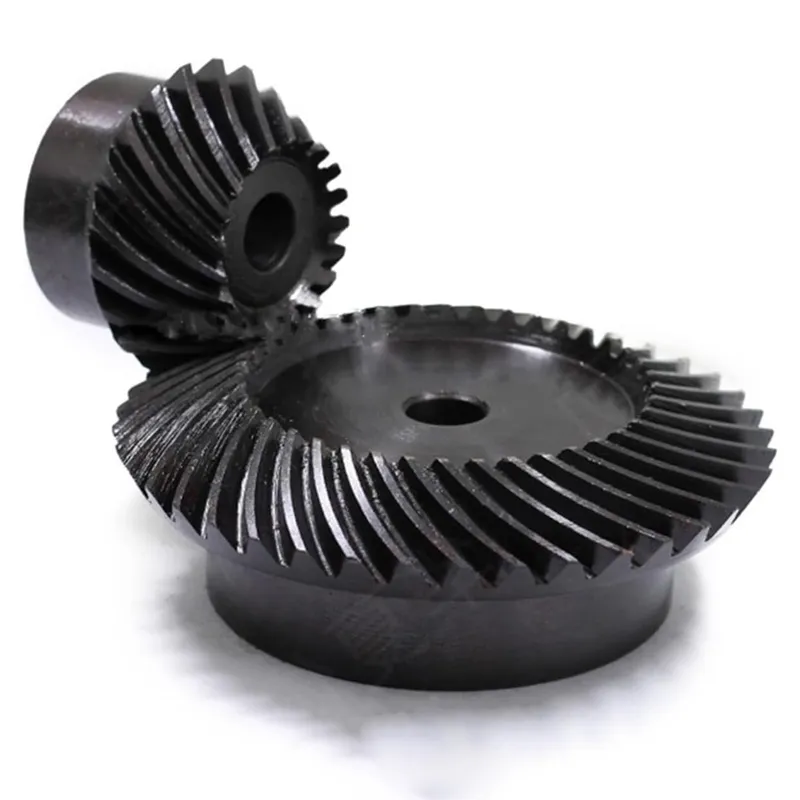
Carbon Steel Bevel Gear
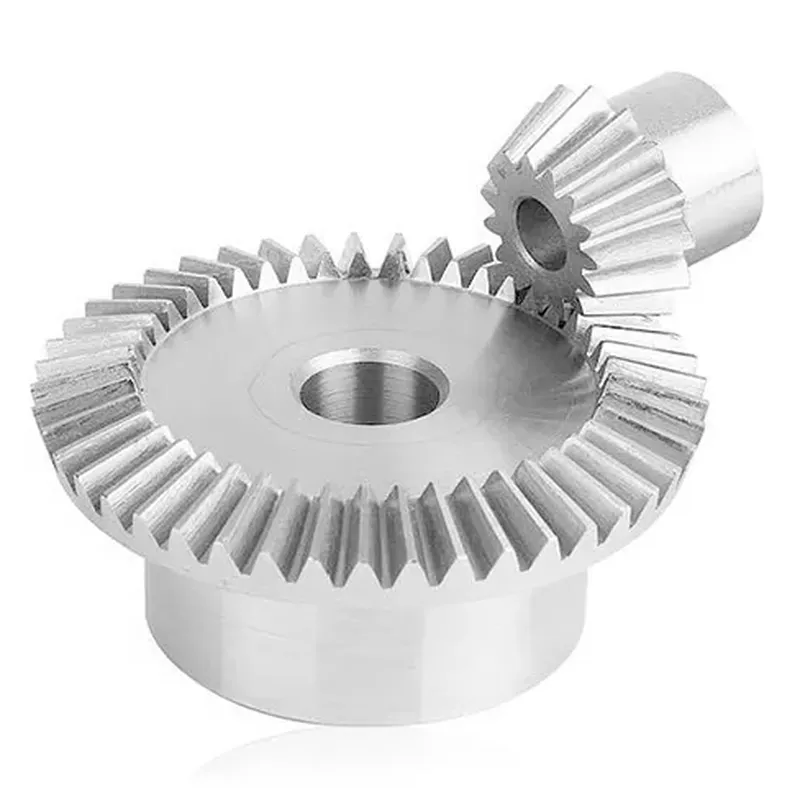
Stainless Steel Bevel Gear
Common Materials of Gear Racks
- Steel
- Carbon Steel: A popular choice due to its strength, durability, and affordability. Cold-drawn steel (e.g., AISI 1045) is often used for precision racks in industrial applications like machinery and automation.
- Alloy Steel: Enhanced with elements like chromium or molybdenum (e.g., 4140, 4340) for higher strength and wear resistance, suitable for heavy-duty racks.
- Hardened Steel: Heat-treated or case-hardened to improve surface hardness, making it ideal for high-load or high-wear scenarios.
- Stainless Steel
- Corrosion-resistant and durable, stainless steel (e.g., 304, 316) is used in environments exposed to moisture, chemicals, or food processing. It’s slightly less strong than carbon steel but excels in harsh conditions.
- Cast Iron
- Typically gray cast iron or ductile iron, it’s cost-effective and offers good wear resistance and vibration damping. Commonly used in large, low-speed industrial racks where precision isn’t critical.
- Brass
- Used in smaller, low-load racks due to its corrosion resistance and ease of machining. It’s less common but found in applications like instrumentation or light machinery.
- Aluminum
- Lightweight and corrosion-resistant, aluminum (e.g., 6061, 7075 alloys) is used in racks where weight savings are important, such as in aerospace or robotics. It’s less durable than steel but sufficient for moderate loads.
- Plastics
- Nylon: Self-lubricating, quiet, and corrosion-resistant, making it ideal for light-duty racks in automation, consumer goods, or noise-sensitive environments.
- Acetal (Delrin): Offers high strength, low friction, and dimensional stability, suitable for precision racks in small-scale systems.
- Plastics may be reinforced with glass or carbon fibers for added strength.
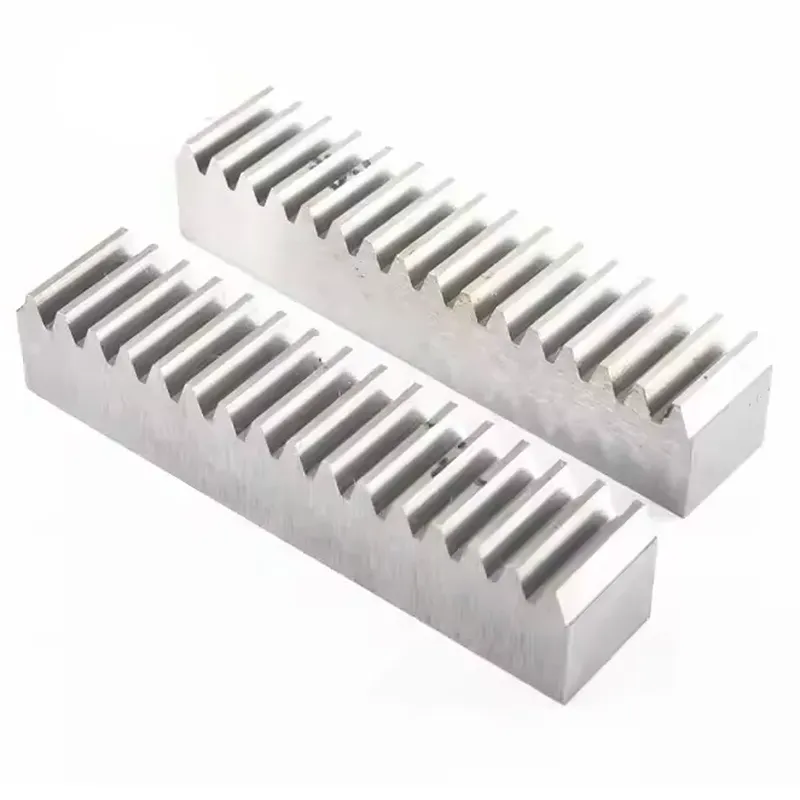
Stainless Steel Gear Racks
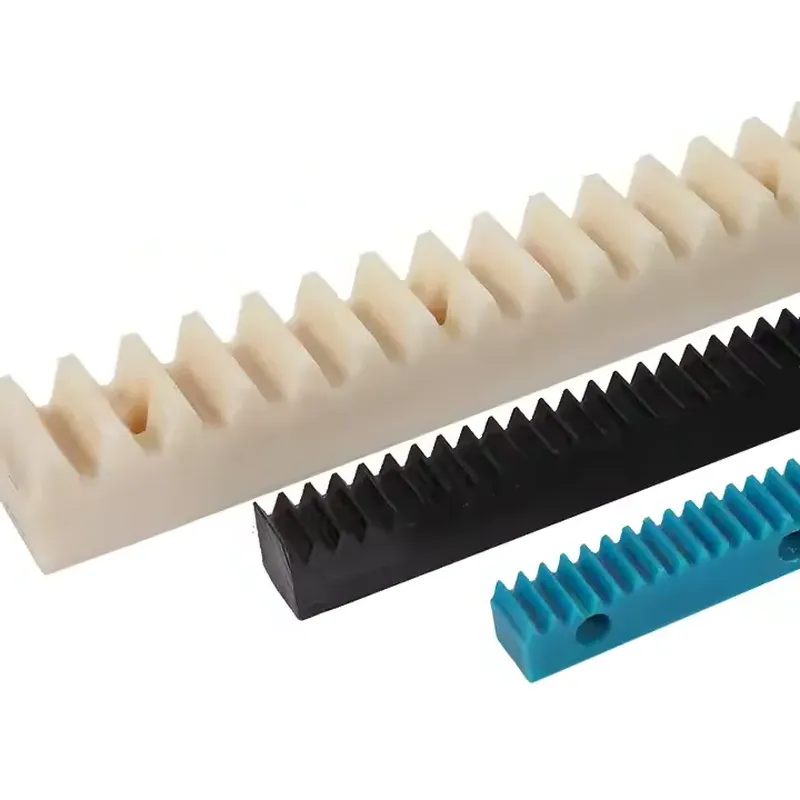